-
POURING MIXTURESPouring the resin mixtures into the mold, the richer resin layer grating will have better anti corrosion performance.
-
LAYING THE GLASSFIBERLay the fiberglass roving crisscrossing into the mold according to the working operation standards, high content of fiberglass leads to high strength of grating.
-
PRESSINGPress the fiberglass certain times at a certain time to remove the bubbles and make glass solid, so that the fiberglass and resin are completely infiltrated, which makes the grating’s structure dense, without bubbles.
A brightly colored FRP grating can improve your production environment, changing the constant grayness of a corrosive environment and adding color to a modern factory.
Shirui's molded FRP grating is high strength, impact resistant, corrosion resistant, fire retardant, anti-slip and anti-aging.
It meets or passes ASTM E-84 fire retardant, Anti-slip R13 (AS4586-2013), DNV, ABS, EU REACH SVHC environmental testing or certification.
We can also produce other grating sizes smaller than the full panel size according to your requirements.
Item No. | Mesh Type | Height(mm) | Mesh Size A×B(mm) | Bar Thickness t1×t2(mm) | Panel Size(mm) | Open Area(%) | Theoretic Weight(Kg/m²) | Figure |
1 | Standard Square Mesh | 13 | 38.1×38.1 | 5.8×5.0 | 1226×3666、1416×4045 | 78 | 6 |
![]() |
2 | 13 | 50.8×50.8 | 5.8×5.0 | 1226×3666 | 82 | 5.8 | ||
3 | 15 | 19.92×19.92 | 5.8×5.0 | 1161×3776 | 50 | 11.5 | ||
4 | 16 | 40×40 | 5.8×5.0 | 1006×4086、1207×4047 | 73 | 7.5 | ||
5 | 23 | 19.92×19.92 | 5.8×5.0 | 1181×3093 | 50 | 20 | ||
6 | 23 | 20×20 | 5.8×5.0 | 1395×3905、1226×4086 | 50 | 18.5 | ||
7 | 25 | 20×20 | 5.8×5.0 | 876×3686 | 50 | 19.3 | ||
8 | 25 | 38.1×38.1 | 6.4×5.0 | 1226×3666、1226×4083 | 68 | 12.5 | ||
9 | 25 | 40×40 | 6.4×5.0 | 1007×3007、1527×4047 | 67 | 12 | ||
10 | 25 | 50.8×50.8 | 7.5×6.0 | 1226×3666 | 80 | 11.8 | ||
11 | 30 | 38.1×38.1 | 6.5×5.0 | 1226×3666、1531×4083 | 68 | 15 | ||
12 | 30 | 40×40 | 6.5×5.0 | 1007×3007、1247×4047 | 67 | 14.5 | ||
13 | 35 | 38.1×38.1 | 6.8x5.0 | 1226×3666 | 68 | 17.5 | ||
14 | 38 | 38.1×38.1 | 7.0×5.0 | 1226×3666、1531×4047 | 68 | 19.8 | ||
15 | 38 | 66.08×66.08 | 9.0×6.5 | 1197×3642 | 81 | 12.5 | ||
16 | 40 | 40×40 | 7.0×5.0 | 1007×3007、1007×4007 | 67 | 19.8 | ||
17 | 50 | 50.8×50.8 | 8.0×5.0 | 1226×3666、1531×4071 | 78 | 23.5 | ||
18 | 50 | 38.1×38.1 | 9.0×6.5 | 1226×3666、1533×4083 | 54 | 32 | ||
19 | 50 | 38.1×38.1 | 7.5×5.0 | 1531×3969、1531×3666 | 64 | 27 | ||
20 | 50 | 38.1×38.1 | 11.0×9.0 | 1266×3666、1420×4049 | 64 | 40 | ||
21 | 60 | 38.1×38.1 | 11.5×9.0 | 1220×3660 | 54 | 50.4 | ||
22 | 60 | 60×60 | 10.0×6.0 | 1510×2410 | 68 | 26 | ||
23 | Micro Mesh | 12 | 25×25(十) | 5.5×5.0 | 1531×4071 | 61 | 7 |
![]() |
24 | 15 | 19×19(十) | 8.0×6.0 | 1226×3666 | 42 | 10.5 | ||
25 | 22 | 19×19(十) | 6.1x5.0 | 1226×3666、1226×4083 | 40 | 13.7 | ||
26 | 22 | 8×8(井) | 7.0×5.0 | 1226×3666 | 70 | 14.6 | ||
27 | 25 | 19×19(十) | 6.5×5.0 | 1226×3666 | 40 | 16.8 | ||
28 | 30 | 20×20(十) | 6.5×5.0 | 1527×4047 | 42 | 19 | ||
29 | 30 | 8×8(十) | 7.0×5.0 | 1000×3000 | 32 | 31.5 | ||
30 | 30 | 8×8(井) | 6.6×5.0 | 1226×3666、1226×4083 | 30 | 19 | ||
31 | 38 | 19×19(十) | 7.0×5.0 | 1226×3666、1531×3969 | 40 | 24.5 | ||
32 | 50 | 25×25(十) | 8.0×6.0 | 1226×3666、1684×4280 | 55 | 28.5 | ||
33 | Rectangular Mesh | 25 | 25.4×101.6 | 6.5×5.0 | 921×3055 | 67 | 14.2 |
![]() |
34 | 30 | 25.4×101.6 | 6.8x5.0 | 921×3055 | 67 | 21 | ||
35 | 38 | 25.4×152.4 | 8.5×6.0 | 1220×3660 | 63 | 22.5 | ||
36 | 38 | 38.1×152.4 | 7.0×5.0 | 1220×3660 | 67 | 16 | ||
37 | 50 | 25×50 | 11.5x9 | 1231×3669、1535×4077 | 42 | 46.5 | ||
38 | 25 | 97.6×38.1 | 7.0×5.0 | 1225×3813 | 83 | 23 | ||
39 | 100 | 93.5×191.5 | 7.0×5.0 | 575×4420 | 88 | 42 | ||
40 | 120 | 186.5×298.5 | 7.0×5.0 | 1500×4190 | 38 | 24 |
Type |
Resin Matrix |
Anti-Corrosion Class |
Fire Retardancy |
Applications |
VCF |
Vinylester |
Chemical grade |
Fire proof,OI>28 |
Acid, alkali solvents and other corrosive environments |
IIF |
Iso |
Industrial grade |
Fire proof,OI>28 |
Medium degree of acid and alkali corrosive environment |
IFF |
Iso-food grade |
Industrial food grade |
Fire proof,OI>28 |
Meat products and other food processing plants |
OAF |
Ortho |
Construction grade |
Fire proof,OI>28 |
General acid and alkali corrosive environment |
OAN |
Ortho |
Constructure grade |
No fire retardancy |
General acid and alkali corrosive environment and no flame retardant requirements |
PIN |
Phenolic |
Industrial grade |
High Fire proof,OI>80 |
High fire resistance, low smoke requirements environment |
Specification |
Category |
Characteristic |
Applications |
E-2400TEX |
Alkali-free roving (E glass) |
Excellent infiltration performance, firmly bonded with the resin matrix, so that the grating has excellent mechanical properties and corrosion resistance |
For high strength and corrosive applications |
Filler type |
Performance |
Applications |
Aluminum hydroxide |
Flame retardant, reinforced, oxygen index 28 or above |
Flame retardant, smoke suppressing environment |
Calcium carbonate |
Reinforced, proper cost reduction |
No fire retardant request |
No filler / pure resin |
Good transparency, corrosion resistance |
No fire retardant request, high corrosion application |
-
Natural Concave SurfaceThe naturally formed crescent grooves(concave surface) give it good anti-slip properties.
-
Gritted SurfaceThe surface of the grating is gritted with quartznds, which makes the anti-slip performance even better.
-
Closed Covered SurfaceThe surface of the grating is decorated with checker or gritted plates to prevent dripping of liquid and evaporation of gas.
-
Smooth SurfaceSurface polishing treatment makes it more delicate and beautiful.
-
Stair TreadsBlack sanding plate at the front end is more eye-catching and safer.
-
Tread Covers
-
Conductive GratingResistance≦108Ω
-
Transparent Gratings
-
Frp Covers(Type 1)
-
Frp Covers(Type 2)
NO. |
Test items |
Test method |
Test result |
1 |
Barcol hardness |
ASTM D2583-13a |
57 |
2 |
Temperature of deflection under load |
ISO 75-1:2013&ISO 75-2:2013 Method A |
〉270℃ |
3 |
Notchless impact strength of simply supported beam |
ISO 179-1:2010 |
290KJ/m² |
4 |
Tensile strength |
ISO 527-1:2012&ISO 527-4:1997 |
217 MPa |
5 |
Tensile modulus |
ISO 527-1:2012&ISO 527-4:1997 |
23600MPa |
6 |
Bending strength |
ISO 14125:1998/Amd.1:2011 |
569 MPa |
7 |
Bending modulus |
ISO 14125:1998/Amd.1:2011 |
23100 MPa |
8 |
Compression strength |
ISO 14126:1998/Cor.1:2011 |
387 MPa |
9 |
Compression modulus |
ISO 14126:1998/Cor.1:2011 |
29300 MPa |
10 |
Shear strength |
ISO 14130:1997/Cor.1:2003 |
33.2 MPa |

Specifications | Span(mm) | Point Concentrated Load(kg) | Line Concentrated Load(kg/m) | Uniform Load(kg/㎡) |
38x38x38 |
1500 | 235 | 305 | 169 |
1200 | 330 | 462 | 370 | |
1000 | 435 | 649 | 720 | |
800 | 611 | 938 | 1410 | |
700 | 748 | 1235 | 2290 | |
600 | 945 | 1680 | 2755 | |
38x38x30 |
1000 | 228 | 288 | 360 |
800 | 310 | 394 | 792 | |
700 | 375 | 475 | 1175 | |
600 | 466 | 590 | 1745 | |
38x38x25 |
1000 | 140 | 150 | 226 |
800 | 197 | 221 | 490 | |
700 | 242 | 277 | 724 | |
600 | 306 | 361 | 1066 | |
20x20x30 |
1200 | 238 | 256 | 262 |
1000 | 315 | 352 | 515 | |
800 | 443 | 522 | 1020 | |
700 | 543 | 660 | 1420 | |
600 | 686 | 865 | 1990 | |
19x19x25 | 1000 | 229 | 216 | 189 |
900 | 241 | 363 | 227 | |
800 | 271 | 531 | 306 | |
700 | 333 | 805 | 376 | |
600 | 352 | 1427 | 495 | |
500 | 484 | 2019 | 609 | |
50.8x50.8x50.8 | 1700 | 345 | 318 | 220 |
1500 | 422 | 398 | 374 | |
1200 | 607 | 594 | 825 | |
1000 | 817 | 825 | 1410 | |
900 | 978 | 972 | 1820 | |
800 | 1175 | 1230 | 2435 |
1.The test block area of point load is 200x200mm.
2.This data is for reference only, there is a 10% fluctuation of loading according to different resin, fiberglass and surface requirements, please contact us if you need relevant detail data as per different type.
3.The specification code 38x38x38 refers to the grating mesh size of 38mmX38mm and thickness of 38mm.
The gratings can be easily cut or perforated with a manual cutter equipped with a diamond cutter blade or even with a regular hacksaw blade, the grating can also be drilled with a driller, but not lathed or tapped.
Certainly, in order to minimize the waste during cutting, the size of the site and the size of the grating should be statistically analyzed before cutting to ensure the maximum economic benefit.
At least 40mm wide supporting is needed each side of the grating. When the grating is used as a trench cover, it can be installed without fixing fasteners because the trench is usually left with a stop, but when it is used as an operational walking platform on the structure, at least 4 sets of fixing clips are required for each grating, and the bottom of the connection between the gratings should be supported by a secondary beam.

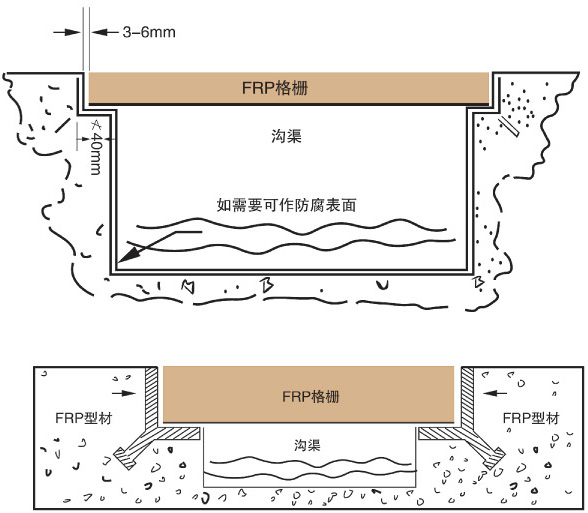
Three popular standard fixing clamps/clips are commonly used for fixing and connecting gratings to frames and gratings to gratings. All clamps are available in either stainless steel or hot-dipped galvanized versions.
-
[ M type Clamp/Clip ]Connecting between gratings and supports, fixed position connection, fixing around.
-
[ C Type Clamp/Clip ]Connecting between gratings next to each other.
-
[ L Type Clamp/Clip ]Special positioning between grating and support.
This requirement is also very reasonable.
We are so proud to offer the best balance relationship between price and performance and are committed to improving the value of our products rather than a momentary low price.